Gemba Walk
What is Gemba Walk
Gemba is Japanese for "real place". In Lean we mean this is the place where the work takes place.
Lean insists on "go see" and Gemba - go see the real place
Through this technique -- leader should go to the floor to observe and collaborate, to know, improve the processes
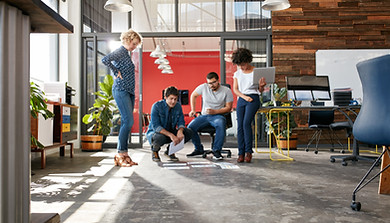
When to do Gemba Walk
-
It's an opportunity for the leader to first hand -know the work, understand challenges, find opportunities for improvement and to share and take best practices to cross-pollinate
-
To do hands-on mgmt
-
Improve engagement
-
To view the process with a different set of eyes
How to do Gemba Walk
-
How long: 45-60 min per period - preferably weekly
-
You may not want to announce or publish a calendar- you want to observe what really happens
-
Do it with a cross-functional team
-
Change teams/ processes every iteration
-
Sit/stand with the worker doing the work
-
Make them comfortable - lower your chair
-
Say - here to learn, be humble
-
Don't correct the worker
-
Use COPIS to get a quick understanding of the process
-
Ask open-ended questions - e.g. so what happens are this, what scenarios do you face, when do you need to stop the work
-
Ask for ideas to improve the process, ask for challenges
-
See are there any of the lean wastes, is every step adding value
-
Also, observe the floor - too many questions, too many distractions, is there energy on the floor..... See what's on the boards
-
Write down what you see, your thoughts - preferably draw a rough process map and notate against it
-
Thank the worker/ team for contribution and time
How to do Gemba Walk
-
How long: 45-60 min per period - preferably weekly
-
You may not want to announce or publish a calendar- you want to observe what really happens
-
Do it with a cross-functional team
-
Change teams/ processes every iteration
-
Sit/stand with the worker doing the work
-
Make them comfortable - lower your chair
-
Say - here to learn, be humble
-
Don't correct the worker
-
Use COPIS to get a quick understanding of the process
-
Ask open-ended questions - e.g. so what happens are this, what scenarios do you face, when do you need to stop the work
-
Ask for ideas to improve the process, ask for challenges
-
See are there any of the lean wastes, is every step adding value
-
Also, observe the floor - too many questions, too many distractions, is there energy on the floor..... See what's on the boards
-
Write down what you see, your thoughts - preferably draw a rough process map and notate against it
-
Thank the worker/ team for contribution and time
Whats next - after Gemba Walk
-
Reflect - with the team - what you saw, observed - was it different from the other teams/ processes
-
What wastes, lack of standard work, ideas did we note
-
Investigate/check facts with the actual doing team - don't assume -- ask
-
Find and agree on areas to work with dates of pilots/ implementation
-
Track the implementation
-
Confirm the implementation and benefits, when you visit the floor
-
If the idea came from a worker - thank and acknowledge